Water Storage Tank Testing and Maintenance Guide
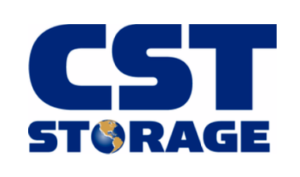
CHAPTER 13 – OPERATION AND MAINTENANCE
(*For HYDROSTATIC TEST PROCEDURE, scroll down to the bottom of section 13)
Continuous and satisfactory operation of the tank requires periodic inspection and maintenance to identify and correct any potential issues as they arise. Below is a minimum recommended inspection that should be completed on a regular basis.
Monthly Inspections
A monthly inspection should be completed by owner or operations personnel. Any discrepancy or sign of damage should be repaired immediately.
- 1 Check for and remove any debris that may have accumulated outside the tank, particularly any debris that is in contact with the tank shell or appurtenances attached to the tank. Remove any mud, oil, or other foreign material on the tank shell.
- 2 Check all seams for any signs of leaks. If a leak is detected, check tightness and tighten all bolts within one-square foot area of the leak. Monitor the area until leak is eliminated.
- 3 Check all seams for any distortion that may have occurred from undue structural stress.
- 4 Check to make sure that there is sufficient drainage away from the tank and no water is standing under or near the foundation.
Annual Tank Inspections (13-1)
An annual inspection should be completed by the owner to ascertain the condition of the tank. The inspection should identify any signs of corrosion, product leakage, coating damage, equipment malfunction, and any other item related directly or indirectly with the performance or safety of the tank. All corrective action should be completed immediately after a problem is identified. In addition to the monthly inspection, the following should be examined.
- 1 Examine the concrete ringwall or slab foundation for fractures that may have developed. Fractures or other distortion can cause eccentric loading on the steel tank and may lead to structural damage or failure
- 2 Check for voids or gaps between the tank bottom and the concrete ringwall or slab foundation that may be caused by foundation settlement.
- 3 Check the anchor bolts and grout (if applicable) to ensure the nuts are tight and grout is not cracked.
- 4 For tanks with granular foundations, check for washouts or other signs of loose or missing backfill.
- 5 Examine the deck for sagging, water standing on the deck, or other foreign material on top of the tank.
- 6 Inspect tank for signs of external corrosion or other coating damage and repair.
- 7 Inspect all fittings and appurtenances for signs of leaking or loose connections.
The appurtenances on the tank should be serviced on a regular basis and inspected annually or more frequently as required.
- 1 Thief hatches (pressure/vacuum) should be inspected and have the seat ring and gasket wiped clean. Check the valve for free movement. In cold environments, inspect for icing caused by condensation. Clean screen of all debris that it has collected. Check for screen deterioration and replace if necessary.
- 2 Free flowing vents should have the screen cleaned of debris and checked for deterioration. Replace if necessary. In cold environments, inspect for icing caused by temperature difference.
- 3 Nozzles and connecting pipes should be checked for distortion of the tank wall at the point of connection or stress within the nozzle or piping caused by settling between the tank and the piping. This situation must be remedied immediately.
- 4 Liquid level indicators should be examined for smooth operation, build-up of foreign material, or signs of float cable wear or damage. Check that all connections are tight. In cold environments, check for ice build-up.
- 5 Visually inspect all valves, sample boxes, sight glass, pressure gauges, and all other appurtenances located on the tank.
- 6 Inspect the external ladder, platforms, and handrails for damage or loose bolts.
- 7 Inspect all lightning rods, conductors and connections.
Periodic Internal Inspections
The tank should be drained and internally inspected initially within the warranty period, and then at least every three to five years thereafter, or more frequently if the owner determines that conditions warrant an internal inspection or if required by local, state, or national laws and regulations.
The owner should provide knowledgeable personnel familiar with tank entry and should follow all safety rules regarding tank entry, including but not limited to isolation of potential energy sources, identification of any potential hazards, and confined space entry procedures.
An internal inspection may require removal of any sediment that has accumulated in the tank and the tank may need to flushed or cleaned out.
Any discrepancy or sign of damage to the tank or coating should be repaired immediately. An internal inspection should include, but is not limited to, the following:
- 1 Check complete interior, including deck structure, underside of deck, internal ladders, interior nozzles and appurtenances, and other structure for signs of corrosion or other damage.
- 2 Check internal coating for signs of wear or corrosion caused by flow of liquid, mechanical damage, or coating failure, or damage caused by stored product.
- 3 Inspect and tighten nuts on the bottom of the tank.
- 4 Examine the deck and deck structure for any distortion or sign of structural stress.
Routine Maintenance (From Section 6)
Inspect the inside coating for discoloration (dark brown or reddish streaking) during routine maintenance. Such discoloration will indicate the presence of an electrical discontinuity in the glass coating or at an exposed edge of the sheet. The amount of rust will appear to be much larger than the electrical discontinuity itself. This rust accumulation should be removed. The damaged area should be lightly sanded with a 100 grit sandpaper and then coated with sealer or 6 mil minimum of touch-up coating as supplied, being sure to overlap the damaged area by at least one inch around the damaged portion.
General (13-3)
After the inspection and all repairs are complete, remove all materials, equipment, and tools and clean the tank as required for product quality.
Inspections can be made by the owner’s personnel or other qualified personnel. If this is not feasible, or the severity of the problem warrants the need, an experienced tank technician can be hired through CST’s Field Service Department.
If any touch-up repairs are required to the coating, CST can provide a standard touch-up procedure based on the existing coating. Contact CST for touch-up procedures and materials.
It is recommended that spare hardware be kept on hand to cover normal maintenance or emergency situations. Because of the many types and sizes of tanks and hardware available, contact CST for your particular application. Generally, parts on hand should include gasket material, caulking, bolts, nuts, and washers. Gaskets and hardware should not be re-used once they have been removed.
Installation of new nozzles or appurtenances or a change of service may void the warranty of the tank. If the tank is being considered for a change of service, the specific gravity of the new liquid must be less than or equal to the liquid previously stored in the tank. It is recommended that any such service or physical changes should be brought to the attention of CST PRIOR to the change.
~~~~~~~~~~~~~~~~~~~~~~~~~~~~~~~~~~~~~~~~~~~
CHAPTER 12 – HYDROSTATIC TEST PROCEDURE
The purpose of the hydrostatic testing of a liquid tank is to ensure that all of the sidewall and bottom joints are sealed by simulating the head pressure of a tank in service by filling the tank with water and visually inspecting the exterior for leaks. Bolted tanks have seams and connections and it is not uncommon to have a few leaks when the tank is first filled.
Leaks can be held to a minimum by:
- ensuring that all gaskets are installed correctly (no debris, folds, orcreases),
- all sealant is applied properly at gasket splices, chime laps, and stavecorner radii,
-
12-4 HydroTec Tank Construction Manual
~~~~~~~~~~~~~~~~~~~~~~~~~~~~~~~~~~~~~~~~~HydroTecTM
Operation & Maintenance ManualSection 1 HydroTec Tank Operation and Maintenance Manual
This operator’s manual is intended to be a guide for the safe and efficient operation of your CST Storage HydroTecTM water storage tank, waste treatment tank, or trickling filter shell. This manual is considered as a portion of the equipment and should accompany the equipment.
The following topics are covered in this manual:
- Safety Guidelines
- Sanitization
- Winter Operation
- Inspection and Maintenance
- Coating Touch-up and Care
Installation and service of HydroTec brand equipment is the responsibility of a HydroTec tank dealer and the equipment owner/operator and not the manufacturer, CST Storage.
CST Storage is continually improving its products. Accordingly, CST Storage reserves the right to change design and/or specifications without notice.
The information contained herein is general in nature and is drawn from sources deemed to be reliable. It is intended for general information purposes only.
The results obtained by the use of these products are dependent upon strict adherence to manufacturer’s instructions for proper operation of the equipment as outlined in the appropriate operator’s manual. In all instances the employment of good management practices in circumstances not specifically referenced in such manuals is required.
CAUTION:
Before using any equipment manufactured or distributed by CST Storage, you should thoroughly study and understand the appropriate Operator’s Manual. If you do not have an Operator’s Manual for a particular item of equipment, one can be obtained through your HydroTec tank dealer. Decals as illustrated and placed on the equipment provide important safety and operating instructions which you should follow whenever using the products.
Your right to copy this manual is limited by copyright law. Making copies, adaptations, or compilation works without prior explicit written permission of CST Storage is strictly prohibited by law and constitutes a violation of the law.
HydroTec tanks are designed and manufactured by CST Storage. These tanks have been designed to specifications supplied by the tank purchaser and/or his specifying engineer. Specific design constraints have been provided by the specifying party including, but not limited to: the density of the stored product, the location of the overflow devices, the filling and emptying means, the design codes controlling the
design of the tank, etc. This specific information has been supplied as an integral part of the submittal package prior to the construction process. You must consider this information as part of your operation and maintenance review.
Specific procedures may need to be generated by you as the tank operator based on a specific need of you, your employees, and others involved in the maintenance and use of this tank. Use of this tank for purposes other than those specified in the original design documents may void your warranty, damage the tank, and/or create the risk of personal injuries or death. Should you have need for specific information not available to you from your files, please contact the installing dealer and/or CST Storage at the address provided.
Section 2 SAFETY GUIDELINES
HydroTec tanks are used for many purposes and can be incorporated into larger storage or process systems. Therefore, other safety related guidelines, in addition to those presented in this section, may be appropriate for your installation. You or your system designers are in the best position to make these recommendations.
General
Access to all HydroTec tanks must be limited to authorized personnel. To deter vandalism or tampering, the owner operator should implement appropriate security measures including, but not limited to: enclosing the tank area with a fence, providing lighting at tank ladders and platforms, installing an alarm system and/or a ladder gate. If the tank has a roof, keep the top manway locked. This manway should be opened by authorized personnel only.
When entering a tank it is your responsibility to comply with the following safety information topics.
RECOGNIZE SAFETY INFORMATION
Look for this symbol, it means… Attention!
Be alert!
Your safety is involved!DANGER:
Tanks may be considered to be “confined spaces” under certain local, state and/or national regulations and standards. You should establish and implement a confined space entry safety program to conform with such regulations, standards, and reasonable safety measures. CST Storage cannot design a program to suit your specific needs and situation.
Many well conceived confined space safety programs include the following:
- Identification of the existence of a “confined space” and the hazard(s) associated with that confined space, i.e., a confined space has a restricted means for entry or exit and has the potential for containing a hazardous atmosphere or other dangerous condition;
- Restrictions on access to a confined space so that only properly instructed and properly equipped personnel enter the confined space;
- The use of various equipment and procedures to control the hazard presented by the confined space, i.e., the use of retrieval lines, respirators or special protective clothing;
- The presence of an attendant outside the confined space to maintain contact with personnel inside the confined space and to monitor events; and
5. Access to properly trained rescue personnel and rescue equipment.
DANGER:
Flammable, explosive, or lethal gasses may be present in and around certain tanks. Do not smoke or allow open flames or sparks in the tank area. Fire or explosion may result. Use an approved breathing apparatus and protective clothing when dangerous gases are being handled or may be present in or around the tank. Failure to heed may cause serious personal injury or death.
Safety Decals
The safety decals that are located on the types of tanks covered in this manual are illustrated. You should inspect each decal or safety sign at least annually. Those which are worn, missing or illegible must be replaced by you. Use the attached graphic display to aid in your inspection. Contact your HydroTec tank dealer if new decals are required.
Section 3 SANITIZATION
(Described for Potable Water Storage Tanks)
Forms of Chlorine
Various forms of chlorine are used for the purpose of sanitizing potable water tanks. HydroTec tanks are constructed using a joint sealant which can be substantially degraded during the curing process by a strong oxidizer such as chlorine. Care must be taken to follow the recommended chlorination procedures to prevent deterioration of the tank joint sealant.
Excessively high concentrations of chlorine will damage the tank joint sealant if granules or tablets are not dissolved prior to their being placed in the tank.
Methods of Chlorination (REFERENCE AWWA C-652)
The American Water Works Association (AWWA) Standard C-652 describes in detail several methods of tank chlorination. Some are more or less appropriate depending upon tank and coating system designs. The chlorination of a tank after construction and prior to being placed in service needs to be coordinated with your HydroTec tank dealer. Specific criteria apply to the cure time requirements for structure sealants prior to the first filling and/or sanitization process.
- The recommended method for chlorination of an HydroTec tank and the method preferred by many tank operators is to fill the tank with potable water to approximately 5% of its volume. Add sufficient available chlorine to this water to attain a 50 milligrams/liter (mg/l) available chlorine level. The chlorine can be added by: injecting gaseous chlorine by use of a gas-flow chlorinator; introducing sodium hypochlorite by chemical feed pump to the inflowing water; or pouring dissolved sodium hypochlorite into the tank from a side manway or roof hatch. Never exceed 50 mg/l concentration for the volume of water actually in the tank. This solution is to be retained for 6 hours. Then, fill the tank to the overflow level with potable water and retain at that level for a minimum of 24 hours. The free chlorine residual after 24 hours must be not less than 2 mg/l.
The highly chlorinated water in the drain piping must then be purged. The remaining water should be tested and certified for acceptable quality according to local health department codes prior to delivery to the distribution system.
- As an alternative method, the tank can be filled with potable water to the overflow level. Enough chlorine must be added so that the available chlorine concentration shall be 10 mg/l at the end of 6 hours, but at no time should the concentration exceed 50 mg/l. The chlorine can be added by injecting gaseous chlorine or introducing sodium hypochlorite by chemical feed pump to assure uniform mixing.
After six hours, the chlorine residual should be reduced to not more than 2 mg/l by a combination of additional holding time and/or draining and refilling the tank with potable water having a lower chlorine residual. The water must then be tested for acceptable quality according to local health department code prior to delivery to the distribution system.
Care should be taken when handling any chemical. Only experienced personnel should attempt to chlorinate the tank contents. Use the utmost care and check local codes prior to disposal of chlorinated water.
Section 4 WINTER OPERATION Minimize Ice Formation
Ice formation in water tanks can cause extensive damage. Interior sealer or coating damage may result from the abrasive action and/or impact of an ice cap moving within the tank with changing water levels.
In any tank, catastrophic structural failure can result from the tremendous forces of ice expansion or the loads created by the weight of ice. Internal accessories, level gauges, overflow weirs, etc., can be ripped from tank walls causing structural damage.
To avoid this type of damage you must limit the formation of ice. There are various devices available to assist in this process, including the use of insulation to control heat loss. It is the owner’s responsibility to determine if the use of this tank requires such devices.
The most widely used method to control ice in potable water tanks is to keep turning over the tank contents. It is recommended that pumping schedules be maintained so that water is kept moving during periods of lowest demand. On a daily basis, at least one third of the tank volume should be turned over. If necessary, water may have to be discharged to allow fresh, warmer water to be added. Take care to discharge water in an appropriate manner.
Additionally, on tanks supplied with a roof, roof damage can occur when ice formations come in contact with the roof. To help minimize the chance of this type of damage, the high water level in the tank should be lowered during the winter months to keep ice formations from contacting the roof.
Thawing a Frozen Tank
A tank which has frozen has a high risk of structural damage. A tank which is no longer operational because of excessive ice buildup must be thawed immediately to limit further damage.
The tank thawing process itself can create substantial risks. Experienced contractors should be employed to carry out the work, usually under the guidance of a consulting engineer. If the tank has experienced an extensive ice buildup requiring a thawing-out process, it should be drained and inspected for damage at the earliest opportunity. Your HydroTec tank dealer can make this inspection and perform repairs at your direction.
CAUTION:
The formation of ice in a tank can result in damage to the tank, its roof (if applicable) and its accessories. The owner/operator must take appropriate steps to limit the formation of ice in the tank.
Section 5 INSPECTION and MAINTENANCE
Inspection and maintenance are important parts of the use of every piece of
equipment. Your CST Storage manufacturer’s warranty may provide for certain maintenance responsibilities as conditions of your warranty. You should carefully review the terms of that document. In addition, the following listed steps will help you provide for the minimum maintenance needs of your equipment.Tank Inspection and Maintenance
Periodic exterior and interior inspections and maintenance are needed to keep your HydroTec tank in proper operating condition.
Exterior — This type of inspection is to be performed yearly and focuses on the exterior portions of the tank. You can do this type of inspection while the tank is in service.
Interior — This type of inspection is to be performed at least every five (5) years and focuses on the interior portions of the tank. You perform this type of inspection while the tank is out of service.
Exterior Inspection (Yearly)
You should inspect the exterior of your tank on a yearly basis. The focus of this section is on those portions of the tank that can be inspected from the exterior, while the tank is in service.
Inspect all safety and information related decals for legibility.
Inspect overflow pipes, overflow weirs, and pipe terminations to assure that they will perform their design function.
Inspect the tank ventilation systems, including screens designed to prevent birds, insects, and debris from entering the tank.
Inspect the exterior coating of the tank for possible damage.
Inspect ladders, locks, platforms, ladder cages, and safety climbing devices (if specified) for corrosion and/or damage.
For each of the above items you should perform any necessary maintenance and repairs as part of the inspection process.
Interior Inspection (Five year interval, minimum)
You should inspect the interior of your HydroTec tank at a minimum interval of five (5) years, or more frequently if and as your experience indicates. The focus of this section is on portions of the tank that should be inspected while the tank is out of service.
Inspect for internal sheet and roof coating integrity, particularly in areas where external damage may have occurred.
Inspect tank/roof coating in general at all fastener locations and at sheet edges.
Inspect the condition of the sealant used in all joints, at the tank wall to floor junction, in the area of sumps, and other tank or floor penetrations.
Inspect the silt stop (if applicable) for function and integrity. Inspect the coating on galvanized parts.
Inspect other interior tank components, riser pipes, level gages, overflow weirs, etc., as appropriate for each device.
Inspect the floor as appropriate for the floor type. Some tank floors are glass coated steel; other floors are coated or uncoated concrete.
For each of the above items, you should perform any necessary maintenance and repairs during the time the tank is out of service for the inspection.
Inspection and Maintenance Documentation
Many successful tank operators have found a maintenance log document to be helpful. Often, forms fulfilling this purpose already exist within the owner’s system and can simply be adapted for this use. The frequency, type of activity, and identity of persons performing maintenance should be reflected in the document. Generate a format that best serves your purposes, with the understanding that such a log will be most helpful to you in providing for the successful operation of your tank.
Tank Cleaning
Potable water tanks should be drained and cleaned at least annually to prevent accumulation of silt and sediment which may affect water quality and damage water meters, valves, etc. Normally a water hose with line pressure water is sufficient. Hot water or cleaning additives are not recommended. Do not use high pressure water.
A plan should be established for maintaining adequate water supply during the time the tank is out of service for routine inspection and cleaning. Cleaning schedules may also be appropriate for other types of HydroTec tanks.
Visual Inspection
At the time of regular tank cleaning, a visual inspection must be made to check the coated sheet for any evidence of physical damage. See Section 6 for coating repair recommendations.
If structural damage is found contact your HydroTec tank dealer for recommended repair methods.
Ladders and Platforms
Ladder, ladder cage, and platform connection brackets must be visually inspected for corrosion or damage at each use. Replace damaged brackets if required. Ladder rungs should also be visually inspected to assure they are safe for use. If a safety climbing device was specified, follow the manufacturer’s instructions on proper care and use.
The installation or use of fixed interior ladders is not recommended as they are susceptible to corrosion and ice damage.
Ventilation For Roofed Tanks
The tank vent is provided to prevent damage to the tank from pressure and/or vacuum created by normal filling and emptying of the tank. It is designed to prevent most birds, insects and debris from entering the tank.
The vent screen must be inspected at least annually. It must be cleared of leaves and debris which would prevent it from functioning properly. The screen can be cleaned by removing the four (4) bolts that secure the top cover. (Two 9/16” wrenches are required.) Lift off the cover and clean the screen thoroughly with a soft brush. Reinstall the cover by reversing the above procedure.
Overflow Pipe
Overflow pipes can become clogged with debris. To prevent entry of birds or small animals, the discharge ends should be screened, provided with a flap valve, or other method of closure. The overflow pipe should be kept clear and checked regularly to be certain it operates freely.
Dome Roof
Some HydroTec tanks may have a geodesic dome roof. The dome must be inspected in accordance with the manufacturers’ requirements.
Section 6 COATING, TOUCH-UP, & CARE
The coating on the HydroTec tank is a durable coating. This coating can, however, be damaged. This section covers the touch-up and repair of the glass coating.
The coating can be damaged by handling or if the coating is impacted. Additionally, some blemishes can occur during the manufacturing process. Although the steel parts are packaged at the plant to prevent shipping damage, some minor damage can occur during the erection process if the sheet is mishandled. Also, during periods of regular service, the coating could be damaged by the impact of sharp tools or by the impact of small projectiles, such as rocks, air rifle pellets or rifle bullets. The coating should be inspected during the regular cleaning cycle and routine maintenance of the tank.
This procedure is designed to cover three possible repair situations:
- Touch-up and repairs during normal erection
- Touch-up and repairs during regular service
- Touch-up and repairs during routine maintenance
Erection Touch-Up
During tank erection, the installation crew is trained to observe the surface of the coating as each sheet is put in place. If, during this erection period, a coating discontinuity or a damaged section is noted, it will be repaired by immediately applying a 10 mil minimum thickness of sealer or 6 mil minimum of touch-up coating as supplied over an area approximately 3 – 4 times the size of the damaged area. No surface preparation is required for this repair. Repairs of this type do not affect the overall warranty of the HydroTec tank. In-Service Repairs
During the normal course of operation of an HydroTec tank, coating damage can happen. Such situations could include:
Vandalism
The impacting of a projectile such as a bullet or thrown object.Accident
The dropping of a small tool from a considerable height and impacting the tank roof or sidewall.The striking of the tank by a large object, such as a fork lift, crane, truck, etc., in which damage might extend over one or more sheets of the structure.
The touch-up or repair of the first of these damages, i.e., the impact of a small tool, would be very light surface sanding with 100 grit sandpaper and then the coating of the damaged area with sealer.
CAUTION:
Any person involved in tank repair or inspection should be trained and equipped in personal safety and confined space entry procedures.
The repair of a sheet or part of a sheet that has been impacted by a projectile can take two forms:
- The first form would be the repair if the projectile did not penetrate the sidewall of the structure. In such a case, the damaged area should be lightly sanded with a 100 grit sandpaper and then coated with sealer or 6 mil minimum of touch-up coating as supplied, being sure to overlap the damaged area by at least one inch around the damaged area. If it is determined during this repair, that the steel has been bent, deformed, etc., there may be similar glass damage on the inside of the structure. This should be touched up as described above. While it is not necessary to do this immediately, as the penetration of any internal rusting will be relatively slow, repair should be accomplished within a year.
- If the side wall of the structure has been penetrated, and the hole size is small, temporary repair can be accomplished by driving a wooden plug in the hole to stop the leak until a permanent repair can be made. To permanently repair this type of damage, drill out the damaged hole to a diameter of 9/16”. Then insert a standard CST Storage encapsulated bolt into the hole along with an appropriate amount of sealer to cover the damaged and unglassed area. Secure the bolt with a washer and a nut similar to the type used to erect the tank. This type of repair will seal the leak. Additional coating touch-up may be required.
If the damaged area is large, i.e., it involves one or more sheets, the tank should be taken out of service at the first opportune time; the damaged sheets removed, and replaced with new sheets. This can be accomplished usually in less than one day’s time by a trained crew employed by an authorized independent Engineered Storage Products Company dealer.
Routine Maintenance
Inspect the inside coating for discoloration (dark brown or reddish streaking) during routine maintenance. Such discoloration will indicate the presence of an electrical discontinuity in the glass coating or at an exposed edge of the sheet. The amount of rust will appear to be much larger than the electrical discontinuity itself. This rust accumulation should be removed. The damaged area should be lightly sanded with a 100 grit sandpaper and then coated with sealer or 6 mil minimum of touch-up coating as supplied, being sure to overlap the damaged area by at least one inch around the damaged portion.
After proper tank construction has been completed, the Owner is responsible to install all manway covers, valves, appurtenances, and blind flanges to cover all openings on the tank.
Once the tank is sealed and water source connected, proceed with filling the tank. Due to a wide variance in the available pressure and flow rates from the supplied water source, the duration required to fill the tank varies.
During the filling process, the tank should be monitored periodically. Any leaks can be repaired as they are discovered. The tank may be filled either to the maximum working level or to the overflow level.
After the tank is full, perform a thorough visual inspection of the shell and perimeter of the foundation to determine if there are any leaks. CST does not recommend a minimum hold time, but it may be beneficial to allow the tank to sit for approximately 24-hours prior to draining or transferring the water to another tank to allow any slow leaks to develop, if any.
The customer or a representative should inspect the tank and accept it prior to draining. The customer or its representative should inspect the tank and accept it prior to draining.
Repair Procedure
If a leak does occur during filling or inspection, the following steps should be followed to repair the leak.
- 1 Check the leaks first which are highest on the tank. What appears to be a leak near the bottom may be coming from a leak higher up.
- 2 Look carefully for the source of the leak since it may follow a seam for some distance before it can be easily seen.
- 3 Carefully tighten the bolts next to a leak for about one foot in both directions. Do not over tighten. It is possible to squeeze the gasket out of a seam, making it necessary to replace the whole strip of gasket. Stop tightening when gasket begins to compress. To tighten evenly, work back and forth from one bolt to another.
- 4 In some cases, leaks are caused by humps in the steel plates halfway between bolts especially on lighter gauge steel. Often the mostand all bolts are visually double-checked to see that washers and nutshave been installed and tightened.Since a tank must be drained to fix a bottom leak, CST recommends that all of the bolts in the floor of a liquid tank be double checked prior to closing up the tank for filling to minimize the potential for a floor leak. Check the floor fasteners manually with a socket and torque wrench for proper torque.
If fiberboard is present under the tank and was wetted by rain during construction, it may take up to a week for the fiberboard to dry out and stop oozing water.
A vacuum box test is an alternative method of checking the floor, but is not considered more conclusive.
Fill Tank and Inspect effective way to stop a leak of this type is to tap the steel around the leak gently with a ball peen hammer.
5. To stop a leak along the thread of a bolt, remove the nut. Replace the combination washer with a two piece seal washer CST part numbers 795NR4000 (rubber O-ring) and 791MR4000 (special washer). Re- install the nut.
277996-000 R1
ECN 12059
© Copyright 2012 CST Storage~~~~~~~~~~~~~~~~~~~~~~~~~~~~~~~~~~~~~~~~~~~~~~~~~~~~~~~~~~
Here is a PDF version of CST’s Tank Operation Manual: